Electric Drive Assembly and Maintenance Workbench—a state-of-the-art trainer designed for comprehensive learning in new energy vehicle technology. Engineered for universities, vocational schools, automotive training centers, and repair companies, this workbench is an essential tool for mastering the assembly, maintenance, and fault diagnosis of modern electric drive systems.
Advanced Training for Electric & Hybrid Drive Systems
At the heart of this training tool is a full-scale replica of the original drive motor and its associated control system. The workbench replicates real-world conditions by providing:
Full System Integration:
- Drive motor assembly and disassembly
- Reducer installation and adjustment
- Electronic control system demonstration with DC power supply
- Simulated operational tests including ignition, gear shifting, acceleration, and braking
Comprehensive Fault Simulation:
The integrated fault setting system allows instructors and students to simulate faults and observe how the drive system reacts. This hands-on approach is essential for understanding troubleshooting techniques and diagnostic procedures.Robust Design & Safety:
Constructed with a sturdy metal frame and equipped with multiple storage and testing zones, the workbench ensures both safety and mobility. Its plug-and-play design means minimal preparation time, maximizing classroom efficiency.
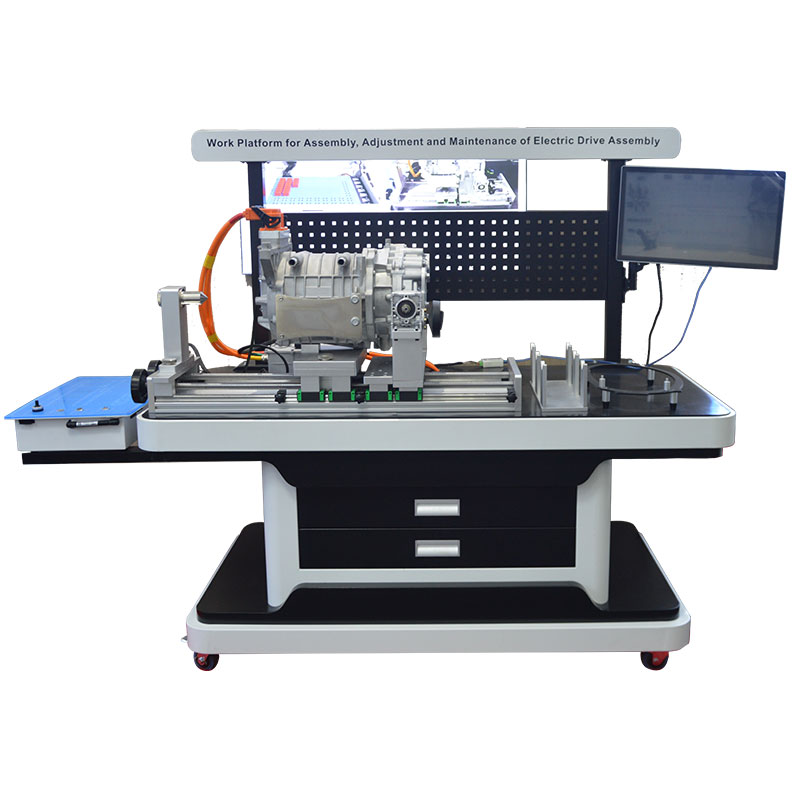
Key Features & Product Configuration
The Electric Drive Assembly & Maintenance Workbench is built with precision and versatility to support various training scenarios:
System Components:
- Drive Motor & Reducer: Mimics real new energy vehicle drive units with parameters designed for practical training.
- Assembly Machine & Flipping Mechanism: Ensure accurate and repeatable assembly operations.
- High-End Control & Monitoring: A dedicated computer host, monitor, and upper computer system software deliver real-time data, enabling interactive learning and effective diagnostics.
- Fault Box & Measurement Platform: Over 80 fault design circuits and high-precision measurement capabilities allow for detailed inspection and troubleshooting.
- DC Power Supply & Desktop Switch: Facilitates safe and controlled power management during testing and maintenance.
Dimensional and Technical Excellence:
The workbench’s overall dimensions and component specifications have been engineered to meet rigorous industry standards, ensuring authenticity in training and ease of maintenance. Every element—from the permanent magnet synchronous motor to the reducer housing fixtures—has been carefully specified to simulate real-world automotive conditions.
Benefits for Instructors and Students
For Instructors:
- Authentic Demonstrations:
Utilize OEM-standard components to deliver real-world training on electric drive assembly and diagnostics. - Enhanced Teaching Tools:
The integrated fault setting system and digital monitoring provide dynamic teaching opportunities that clearly illustrate complex drive system functions. - Efficiency and Flexibility:
With a design that supports quick resets and minimal setup, lessons can start promptly and run smoothly.
For Students:
- Hands-On Learning Experience:
Gain practical skills in disassembly, assembly, inspection, and repair of electric drive systems—a must-have expertise in today’s electric vehicle market. - Interactive Diagnostic Training:
Learn to interpret live diagnostic data via the OBD II-like interface and master fault identification and correction techniques. - Career-Ready Skills:
The workbench not only builds technical knowledge but also enhances troubleshooting abilities, preparing students for careers in automotive repair and advanced electric vehicle technology.
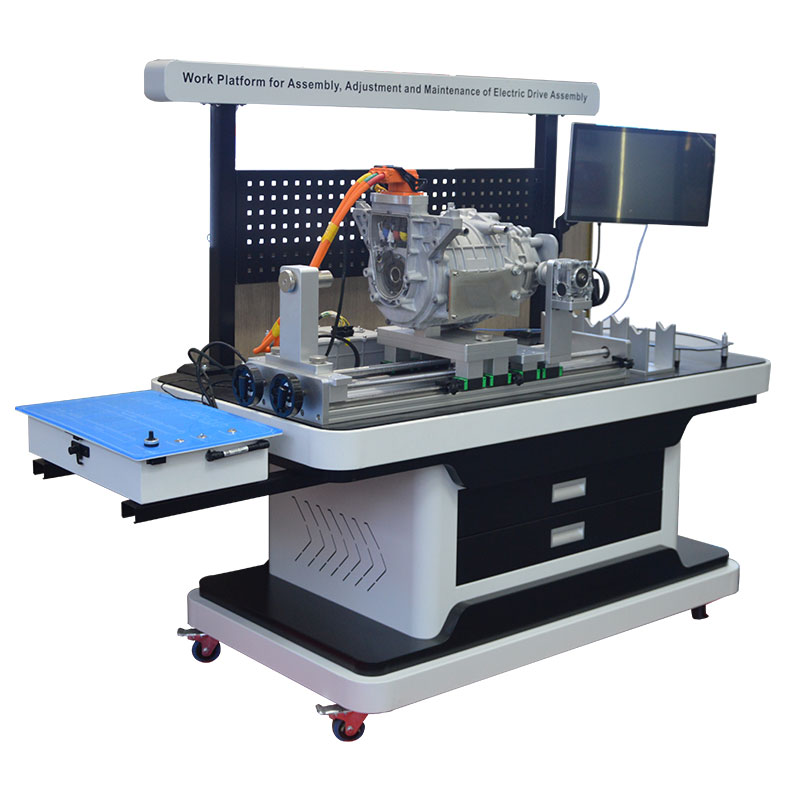
Integration into Modern Automotive Training
Richter is committed to aligning our training equipment with the latest industry trends. Our Electric Drive Assembly & Maintenance Workbench is a vital addition to our range of Automotive Trainers, Electric Vehicle and Hybrid Trainers, and Automotive Simulation Training Software. In close collaboration with renowned automotive manufacturers and educational institutions worldwide, our products are designed to meet the evolving needs of both students and professionals.
With our workbench, you can expect:
- Real-Time Data Monitoring & Analysis:
Utilize integrated software and high-end computing to analyze system performance. - Fault Simulation & Diagnostic Mastery:
Prepare for the complexities of modern electric vehicle maintenance through controlled fault settings and dynamic testing. - Flexible Training Modules:
Adaptable setups that support individual and group training sessions, ensuring a collaborative and engaging learning environment.
Why Choose Richter?
Richter’s reputation as a world-leading manufacturer of automotive and electric vehicle training equipment is built on innovation, quality, and a deep understanding of industry needs. Our training solutions—ranging from automotive trainers and simulation software to smart manufacturing tools—empower educational institutions and repair companies to elevate their technical capabilities.